Lineman Disaster Recovery Stories: Hurricane Sandy
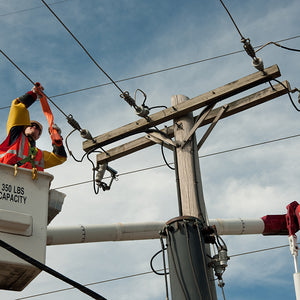
The Atlantic Hurricane Season lasts from the beginning of June to the end of November, reaching its greatest intensity between August and October. The hurricane seasons of the past few years saw some of the most destructive hurricanes on record, which led to some of the most demanding storm recovery efforts.
Electrical linemen are among the most important storm recovery workers, because hurricanes often damage or destroy huge sections of the electrical grid, and other recovery operations require electricity to work at full capacity. I had the chance to talk to several linemen about their experiences in recovery after hurricanes and other natural disasters. In our last blog entry, we shared the story of DJ, a lineman from Virginia. Now we have the story of Matt, another lineman from Colorado.
Matt—Xcel Energy
Hurricane Sandy became the second-most destructive hurricane recorded in the United States when it struck the East Coast in 2012. Hurricane Sandy was also the largest hurricane on record, as it reached a diameter of 900 miles. As it moved up the east coast, it brought rain and hurricane-force winds to the entire eastern seaboard from Florida to Maine, and its effects were felt as far west as Wisconsin.
Sandy made landfall as a Category 1 Hurricane in Atlantic City and Brigantine, New Jersey, on October 29. The storm brought more than 11 inches of rain in some locations, with wind gusts up to 90 miles per hour and a storm surge around five feet. Flooding caused the most destruction, and New Jersey alone saw $36.8 billion worth of damage. More than 2.4 million homes in the state were without power after the storm.
Linemen came from across the country to aid local utilities in their recovery operations, including Matt Mackler from Xcel Energy in Boulder, Colorado. Matt and the other linemen arrived in New Jersey shortly after the storm ended, when the destruction was at its greatest and conditions were at their worst.
Much of the area was still flooded, and where there wasn’t still water above the ground, the ground was still extremely soggy and muddy. Storm debris was scattered over roads and lawns, and wreckage was blocking roads and obstructing access to power lines and worksites. The National Guard and FEMA had cleanup operations underway, but with so many people without electricity, the utility crews didn’t have time to wait for the cleanup to be finished.
Because of the rough conditions, Matt and the other linemen had to spend a significant amount of time clearing debris before they could begin repairing power lines. Each day, the crew met early in the morning where they were assigned a specific circuit and drew up a plan for the day’s work. Then they would spend the next 16 hours clearing fallen trees, furniture, building materials, and other debris, then repairing the damage to power lines and poles.
Matt told me that one of the most important tools he used during the recovery was the handline. There were a lot of power lines that had to be put back up at the tops of the poles, as well as other material that had to be carried up the poles. Rather than carry materials to the tops of poles by climbing up and down repeatedly, he and the other linemen would use the handlines to hoist materials up and keep the recovery moving as quickly as possible. Another important tool he used frequently was his Lug-All Come Along Ratchet Winch Hoist. He and the other linemen used Lug-All winch hoists for pulling up wire and tensioning the lines, as well as clearing debris and even pulling out uprooted trees that were blocking the way.
The three weeks Matt spent on this job were very different from his usual workdays for a few reasons. He and the other linemen were working closely with FEMA for most of the duration of their stay. Close coordination between the linemen and recovery crews was crucial to a complete and efficient operation.
He also noted that customer interactions were very different from typical days on the job. With so many people without power, some customers had a long wait before theirs was restored, and many customers were extremely relieved and grateful to see the line crews working in the area. But he said one of the most rewarding parts was the time spent with the crew.
Many of the linemen I talked to expressed that their fellow linemen were more like brothers than coworkers. This relationship can be attributed to the nature of the work they do; linemen need to have a lot of trust and confidence in each other to ensure their safety when working with potentially dangerous power lines. When you take that kind of work, then spend three weeks of working grueling 16-hour days so far from home, that sense of brotherhood is amplified even more.
To share your story, contact jmiller@spanco.com